New Toy Furniture?
David Hicks | Published on 2/20/2024
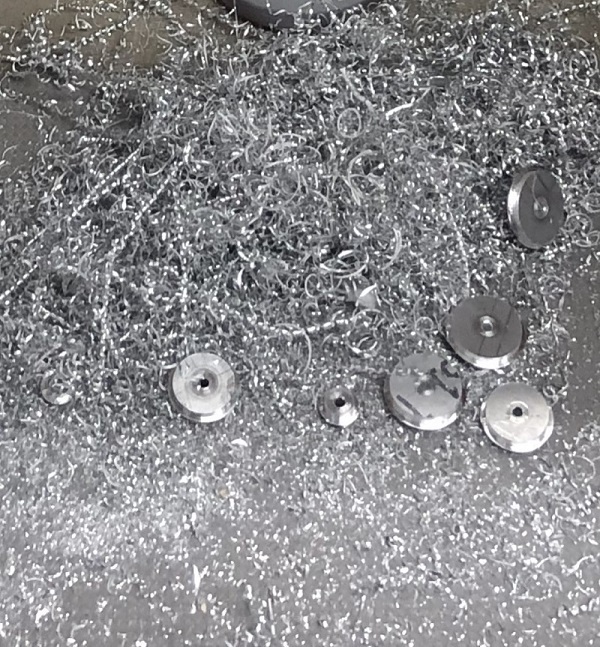
March, 2023 New Toy DIY Wall Mounted Turntable Shelf With Light Show
By David Hicks
Can a piece of furniture qualify as a new toy? Can something bolted to the wall count as furniture? I think so. Especially if it improves the sound of your audio system, or in my case, improves the sound by letting me move and walk around the room when I am playing a record.
I am not the first person to have issues with framing in their home that renders playing records an experience that must be accompanied by pointedly cautionary movement in the room while the needle is riding the groove. There are a few wall mounted turntable shelves available commercially, though not as many as I expected to find given the resurgence of vinyl records and turntable sales. Anyway, I wanted something a little different than anything that I could find ready made for sale. First off, I wanted the shelf to extend 30 inches from the wall. If you look at the picture (below) of my gabled roofline, you can see that having a turntable positioned too close to the wall poses a problem if I wanted the shelf mounted at a height that wouldn’t necessitate stooping over to play records. And, I wanted the shelf to somewhat match the acrylic look of my Stillpoints rack. In fact, I had the idea that the shelf should extend just above the top shelf the Stillpoints, and given that my rack sits out away from the wall for easier access behind the rack, that translated into the 30-inch extension.
Media room, 21’x23’. Above the garage. 8 foot ceiling that is 6 feet wide before the downslopes that taper to 33” from the floor at the side walls.
I knew I would need a thick piece of plexiglass to sustain its rigidity without worries of it cracking. And that meant I would need a substantial piece of mounting hardware to place on the wall to hold the nearly 30 lb. acrylic plexiglass. So, I came up with the design below.
Though I loved the idea of having someone else make the shelf and the shelf bracket for me, I eventually decided that as long as I was retired, I might as well go the DIY route. Plus, as my projects go along they tend to evolve, which just means I can never accurately calculate the cost of having someone else do the work for me.
I bought the aluminum in roughly the size that I wanted and trimmed it with a non-ferrous blade on my table saw so that the pieces fit my design.
With the plexiglass in place but still in the clamp up stage.
Drilled aluminum now bolted together.
The aluminum at this point weighed 22 lbs. I wanted to lighten the piece and give it a bit more aesthetic appeal.
Some design possibilities mapped out with round paper cutouts representing where the holes might go that I would have to drill.
New bits for the modifications.
The first rough cuts.
A little sanding and polishing. The combined weight of the pieces was now lightened by 3 lbs.
And now on to drilling the hole through the plexiglass. The hole is centered in the back at the wall side of the shelf for passage of the tonearm cable and the turntable motor power cable.
I thought it best to practice on a scrap piece of plexiglass.
I looked online and observed some YouTube videos related to drilling through plexiglass. There were lots of tips but none of the examples concerned plexiglass anywhere near this thick (1.25”).
There are two different types of drill bits now stuck in the scrap plexiglass.
For getting stuck bits out it was recommended that you warm the plexiglass in an oven for 20 minutes at low heat. Reading the posts on removing stuck drill bits was actually much more informative than reading the posts about how to drill the plexiglass.
The problems occur when the drill bit heats up the plexiglass and melts the shavings the bit is removing and those melted shavings then cool and harden behind and inside the bit, getting the bit stuck. After my experience with the scrap plastic, I used a home forehead thermometer to frequently check the temperature as I went along.
Definitely a stopping point (below). Some online posts suggested you could just flood the hole with cool water as you went along, but I elected not to flood my workbench with water from a garden hose at the same time I was drilling.
Anyway, in the end I got the hole drilled without too much adventure, but it was a very slow process. I would remove shallow layers a little at a time and let the plexiglass cool in between.
The back plate secured to the wall.
Assembled with the plexiglass and a test of the LED lights mounted in the bracket behind the plexiglass. To make the lighting show up more prominently I stopped the edge sanding at 1500 grit sandpaper and did not polish any further.
With the rack placed underneath the shelf. The dancing girls were holiday gifts from friends in the Rogue Valley.
I can now not only walk around the room while a record is playing but I can dance directly in front of the shelf with no audible effects other than my noisy foot shuffling.